Table of Contents
Productivity is an important metric for businesses. It measures the amount of output employees produce in a specific time frame.
Productive workplaces positively impact the economy and can ladder to a higher standard of living for citizens in the country. Factors influencing this metric include workforce skills, technology development, and management strategies.
Integrating API Pumps into Your Manufacturing Process
API pumps are ideal for the petrochemical industry, given their stringent standards. The API 610 12th Edition standard has strict requirements for allowable shaft deflection, bearing design, casing thickness, flanges, and weldments. It also has specifications for the lubrication system, including an inner slinger to optimize bearing lubrication and a finned upper bearing housing surface to improve heat dispersion.
Despite their rigorous standards, API pumps can also be used in non-refinery applications. However, every pump application presents its unique conditions. Therefore, the off-the-shelf API spec is only sometimes appropriate (100% adherence to this standard may even result in an over-spec’d pump for the application).
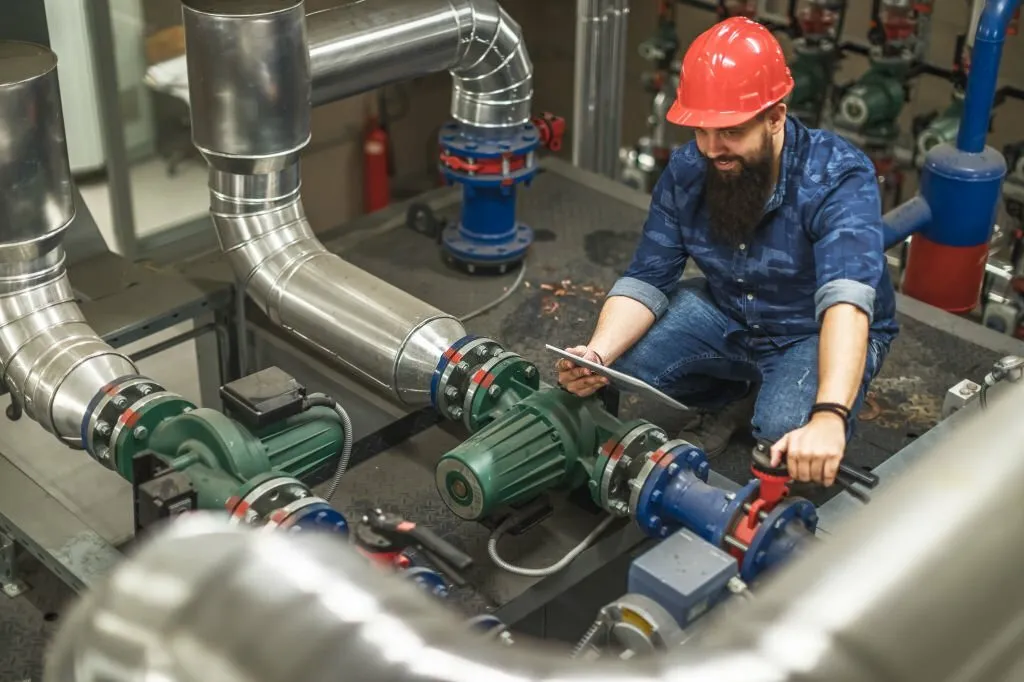
Integrating API Pumps into Your Process
The American Petroleum Institute (API) maintains more than 700 standards that improve the oil industry’s safety, environmental protection, and sustainability.
In addition to their compliance with the API 610 standard, these centrifugal pumps are ideal for use in refinery industries. These pumps’ casings, bearing housings, mounting feet, and back cover arrangements are designed to maximize efficiency in oil refineries while controlling emissions and safely handling hydrocarbons.
They can also handle other fluids, such as sulfuric and hydrofluoric acids, caustics, solvents, and water services, which are common in many industries. However, while ANSI process pumps work well for most applications, they could perform better when handling thicker and highly viscous materials. Unlike ANSI pumps, these API-style pumps are designed to move such materials while providing high reliability under rigorous operating conditions.
Pump Selection
Pumps convert mechanical energy into a force to move the medium through pipework and other equipment in a plant. This force is known as the head. The pump must generate enough charge to overcome the resistance of all the system’s pumps, valves, fittings, and other equipment and meet its normal operating point (BEP).
While ANSI standards focus on dimensional specifications, API standards are more concerned with the construction, design, and ability to handle higher temperatures and pressures. They are also better equipped to handle fluids that are prone to cause environmental damage.
Pump selection and installation are processes that must be done properly for the overall success of your plant. Most facilities operate under tight budgets and need more time for pump analysis. This often leads to a “best guess” system design that oversizes the pumps and adds several safety factors. A well-sized, correctly selected, and installed pump can consume less energy, operate more efficiently and reliably, minimize life-cycle costs, and significantly decrease repair costs.
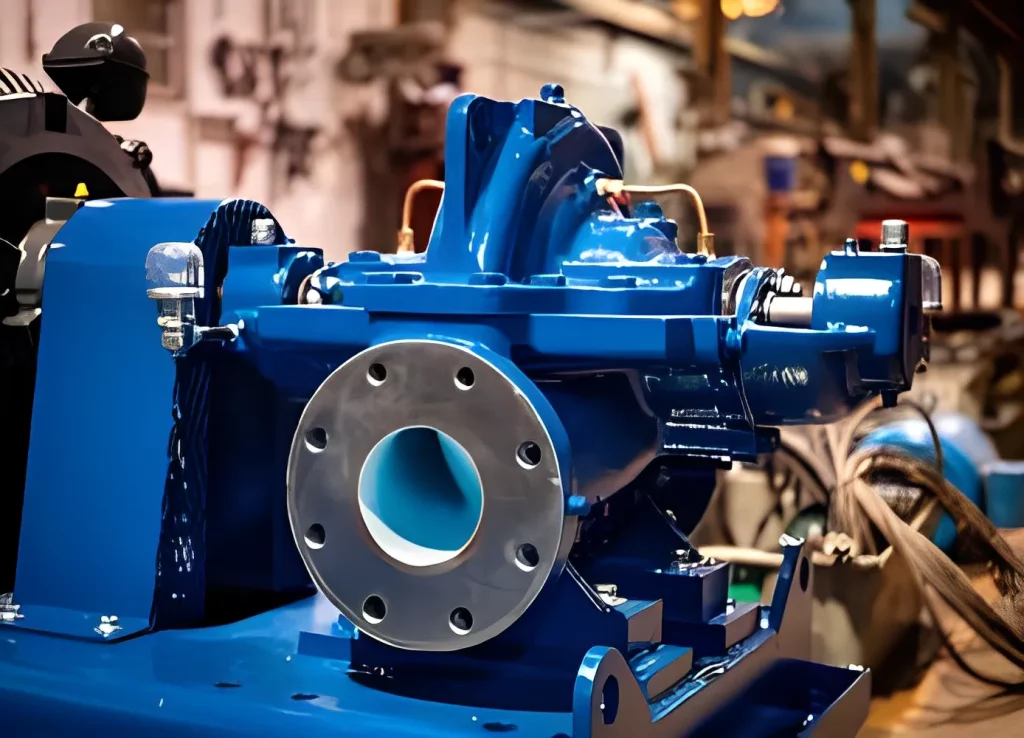
Pump Installation
Often overlooked, energy costs can dwarf the initial capital cost of a pump. This is especially true for systems that must be sized correctly and operating far from their best efficiency point.
Pump manufacturers are incorporating advanced technology to reduce energy usage. These include new motor designs that use larger copper windings to minimize electrical losses and smart controls that automatically adjust the motor speed based on user demands.
These advances also enable a better “wire to water” conversion, minimizing the energy from the power source to the fluid flowing through the pump. These innovations can cut energy costs by up to 20 percent, resulting in significantly shorter payback periods.
Closed-loop controller technologies allow multiple pumps to operate on the same control panel. They can be programmed with different run modes and are password-protected to prevent involuntary changes. One feature, proportional mode, allows two pumps to operate from the same analog input signal. This functionality can help dispense repeatability within 1 percent and higher productivity levels.